Essential Tips to Minimize Risk of Loss in Building Materials Manufacturing
Emily Buchan
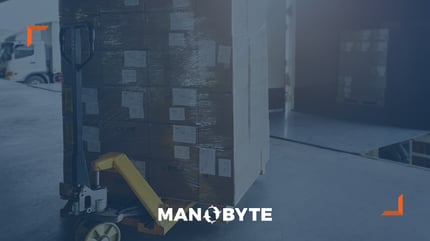
As a business owner, it's natural to want to do everything in your power to prevent damage to your products while they're in transit. Still, despite your best intentions, sometimes things just don't go how you'd planned.
Even if it is nobody's fault, damages still happen—and someone has to pay for it. But thankfully, there are a number of steps that you can take as a building materials manufacturer to minimize the risk of product loss or, at the very least, determine who is responsible for that risk when nobody is expressly at fault. You just need to keep a few key things in mind.
What is Risk of Loss? Breaking Things Down
The term "risk of loss" means exactly what it sounds like—it identifies who bears the risk if goods that are transported are either lost or destroyed even if neither party is specifically at fault.
According to the CISG, Article 66, the loss of or damage to the goods in question after the risk has passed onto the buyer does not actually discharge him or her from their obligation to pay for prices associated with those risks. This is true unless the loss or damage in question happened due to some act or even an omission from the seller.
To take that one step further, the Uniform Commercial Code is a series of laws that is also designed to create both uniformity and predictability among goods being transported in those states who actually observe it. Under the UCC, goods are defined as "movable, tangible items that have been manufactured and offered for commercial sale by a merchant," which in this case would be your building materials manufacturing business.
Types of Contracts Regarding Risk of Loss
If the goods were damaged prior to your client actually receiving them, the liability for the risk will depend entirely on the contract that you signed with that entity.
Two common contracts that fall into this category include:
- Sale on approval contracts: This is when the risk of loss stays with you as the seller until the buyer expressly accepts the items. Keep in mind, however, that any buyer's "trial use" of those materials does not automatically mean that they've accepted them. Under a sale on approval contract, if the buyer decides to make a return, you bear both the risk and the expense for that return. Still, the buyer still needs to follow any reasonable instructions that you make.
- Sale on return contracts: This is common in situations where your buyer is accepting your building materials with the express intention of selling them on to someone else. Here, the risk of loss is passed directly onto the buyer as opposed to your company who is selling building materials, and they will be the ones dealing with both the risk and expense of returning the materials should that be necessary.
Tips For Minimizing the Risk of Loss
There are a few different ways that a manufacturer can proactively improve their processes and systems to help minimize the risk of loss moving forward. Just a few examples of techniques to explore include but are not limited to ones like:
- Conduct a comprehensive audit of your existing training processes to help make sure that staff members with specialized jobs (like packout and loading) are following standard operating procedures. In addition to minimizing the risk of loss, this also helps produce more consistent results.
-
Choose the right packaging materials—and the correct size of that packaging. Not only should your packaging be large enough to carefully hold all shipment contents, but it should have room for the type of impact protection materials that will likely be necessary as well.
-
Make sure all trailers, freight, and other shipping vehicles are loaded properly to begin with. If you're working with a third-party carrier for shipping and transit, familiarize yourself with their standard operating procedures to ensure your shipments are safe.
Mitigating Risk with More Effective Construction Supply Chain Management
All of these situations are why manufacturing risk management and assessment is of paramount importance. Before you can truly take steps to address the types of risks you'll be exposed to during shipping, you need to understand both the nature and severity of those risks as much as possible. This is especially true in regard to the expansive and often global supply chains that most building materials manufacturers are dealing with.
Even one shipment of goods that is lost or damaged in transit can cause major disruption to your normal operations. This is very closely tied to a related concept called production risk, which involves any production-related task that has a broad range of possible outcomes. Production risks can not only include factors like:
- Weather and climate changes
- Disease outbreaks
- Technology mishaps
- Issues with machine efficiency
Even something totally unpredictable like the recent issue with the Suez Canal could have major ramifications on your supply chain. Earlier in 2021, a vast container ship became stuck in the canal for six days due to unusually high tide—causing global supply delays as a result.
In the end, one must acknowledge that especially in an industry with as many moving parts as manufacturing, risk is never something you'll be able to totally eliminate regardless of how you try. But with the right, proactive construction supply chain management strategy in place you can help reduce your exposure to those risks as much as possible—which really is the most important benefit of all.